في حياتنا اليومية, غالبًا ما يلفت أناقة حقيبة جلدية مصنوعة جيدًا, بمثابة ملحق وظيفي وقطعة بيان. الفن وراء هذه الحقائب رحلة رائعة, الكشف عن تعقيدات عملية صنع الأكياس الجلدية. في دليل صنع, سوف نستكشف المراحل المختلفة المتورطة في صياغة هذه الحقائب الرائعة. دعونا نكتشف التقنيات والمواد التي تجعل هذه الملحقات مميزة حقًا.
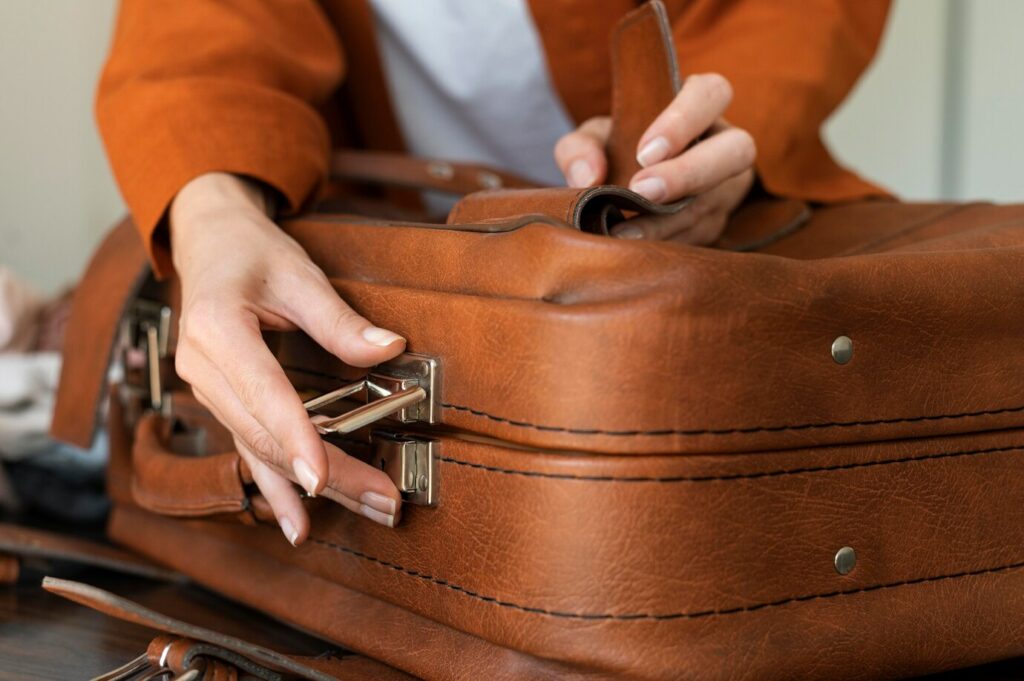
أنواع الجلود شائعة الاستخدام في تصنيع الأكياس
لا يؤثر اختيار الجلود في تصنيع الأكياس على النداء الجمالي ووظائف المنتج النهائي فحسب ، بل يعكس أيضًا قيم الاستدامة والمصادر الأخلاقية. عندما يصبح المستهلكون أكثر وعيًا بالبيئة, فهم مختلف أنواع الجلود ويصبح تأثيرها ذا أهمية متزايدة. دعنا نتعمق في أنواع مختلفة من الجلود شائعة الاستخدام في تصنيع الأكياس, بدءا من بعض الخيارات الشعبية.
جلد الألياف الدقيقة
جلد الألياف الدقيقة, في كثير من الأحيان يعتبر واحد من أفضل جلد لصنع الحقائب, هي مادة اصطناعية مصنوعة من الألياف المنسوجة بدقة. إنه يحاكي نسيج ومظهر الجلود الأصلية مع تقديم مزايا ملحوظة مثل المتانة, مقاومة الماء, وسهولة الصيانة. بالإضافة إلى ذلك, عادة ما يستهلك إنتاجه موارد أقل, مما يجعلها خيارًا أكثر ملاءمة للبيئة مقارنة بالجلد التقليدي. هذا المزيج من الجاذبية الجمالية والاستدامة جعلت من الجلد الدقيق شعبية بشكل متزايد بين المستهلكين الواعيين للبيئة.
بو الجلود
البولي يوريثان (بو) الجلود هو بديل اصطناعي آخر اكتسب شعبية في صناعة الأزياء. إنه يوفر مظهرًا يشبه الجلود بتكلفة أقل, جعلها خيارًا جذابًا للمستهلكين الواعين بالميزانية. لكن, في حين أن جلد PU يكون أكثر بأسعار معقولة وأسهل للتنظيف من الجلد الحقيقي, يمكن أن تكون عملية الإنتاج كثيفة الموارد وقد تتضمن مواد كيميائية ضارة. هذا الاعتبار البيئي أمر بالغ الأهمية لأولئك الذين يبحثون عن خيارات أكثر استدامة في تصنيع الأكياس.
جلد الحبوب الكاملة
يُعتبر جلد الحبوب الكامل أحد اللباح الأكثر جودة متوفرة. يحتفظ بالحبوب الطبيعية والعيوب في الاختباء, تقديم شخصية فريدة ومتانة استثنائية. متأخر , بعد فوات الوقت, جلد الحبوب الكامل يطور زنجارًا غنيًا, تعزيز جمالها وجاذبيتها. بالإضافة إلى, عندما مصادر بمسؤولية, يمكن أن يكون اختيارًا مستدامًا للبيئة, لأنه غالبًا ما يأتي من الدباغة الأخلاقية التي تعطي الأولوية لرفاهية الحيوانات والموارد الطبيعية.
جلد الحبوب العليا
يشبه جلد الحبوب العليا الحبوب الكاملة ولكنه يخضع لعملية لإزالة العيوب, مما أدى إلى الانتهاء أكثر سلاسة. في حين أنه قد لا يمتلك نفس الشخصية الوعرة مثل الحبوب الكاملة, لا يزال جلد الحبوب العليا متينًا وجذابًا. يتم استخدامه بشكل شائع في السلع الفاخرة ويمكن الحصول عليه بشكل مستدام, جعلها خيارًا قابلاً للتطبيق للعلامات التجارية الواعية بيئيًا.
جلد البقر
جلد جلد البقر هو واحد من أكثر الجلود استخدامًا على نطاق واسع في تصنيع الأكياس بسبب تنوعه وقوته. يمكن الانتهاء من هذا الجلد المتين بطرق مختلفة لتحقيق قوام وأنماط مختلفة, مما يجعلها مناسبة للتصميمات غير الرسمية والرسمية على حد سواء. الممارسات المستدامة في مصادر جلد البقر يمكن أن تقلل من تأثيرها البيئي, وضعه كخيار موثوق للمصنعين الذين يسعون إلى تحقيق التوازن بين الجودة مع الصداقة البيئية.
جلد العجل
يتم تقدير جلد العجل لنعومة وملمسه الدقيق, مما يجعلها خيارًا فاخرًا للأكياس الراقية. شعورها الرقيق ومظهره الأنيق يلبي احتياجات السوق الفاخرة, حيث تكون الجودة أمرًا بالغ الأهمية. في حين يمكن الحصول على مصادر أخلاق, من الضروري ضمان إعطاء أساليب الإنتاج أولوية لرفاهية الحيوان والاستدامة البيئية.
جلد جلد الغزال
من جلد الغزال, تتميز بنعومة, الملتوية, يضيف نسيجًا فريدًا واهتمامًا بصريًا بالحقائب. على الرغم من أنها أقل متانة من الأنواع الجلدية الأخرى, سحرها الجمالي لا يمكن إنكاره. يمكن أن يكون التأثير البيئي لإنتاج جلد الغزال مهمًا, لذا فإن اختيار جلد الغزال من المصادر ذات السمعة الطيبة التي تعطي الأولوية للممارسات المستدامة أمر بالغ الأهمية للمستهلكين الواعيين للبيئة.
خصائص الجلود عالية الجودة للأكياس
يمكن للسمات الجلدية أن تؤثر على طول عمر الكيس وتعزيز وظائفها وجاذبيتها الجمالية. دعنا نستكشف ثلاث خصائص أساسية تميز الجلود عالية الجودة: متانة, المرونة, والملمس.
متانة
تقف المتانة كواحدة من أهم العوامل في تقييم جودة الجلود للأكياس. يجب أن تقاوم حقيبة جلدية تم بناؤها جيدًا على التآكل اليومي مع الحفاظ على سلامتها الهيكلية. الجلود عالية الجودة, مثل الحبوب الكاملة والحبوب العليا, تشتهر بمتانة وقدرتهم على مقاومة الخدوش, مجففات, والتدهور العام مع مرور الوقت.
المرونة
المرونة هي خاصية أساسية أخرى تساهم في الجودة الشاملة للأكياس الجلدية. يجب أن يكون جلد الألياف الدقيقة عالية الجودة مرنًا بما يكفي للسماح للكيس بالتكيف مع محتوياته مع الحفاظ على شكله. هذه المرونة لا تعزز الراحة فقط أثناء الاستخدام ولكنها تزيد أيضًا من وظائف الحقيبة. على سبيل المثال, يمكن أن تستوعب حقيبة جلدية مرنة مجموعة من العناصر بسهولة, من أجهزة الكمبيوتر المحمولة إلى الضروريات الشخصية, جعلها مناسبة لمختلف المناسبات وأنماط الحياة.
نَسِيج
يؤثر نسيج الجلد بشكل كبير على جاذبيته الجمالية وتجربته عن طريق اللمس. يعرض الجلود الممتازة نمط حبوب فريد, التي يمكن أن تختلف من الدقة, القوام الطبيعية للجلد الكامل للحبوب إلى النهاية السلسة للحبوب العليا. يجب أن تدعو حقيبة جلدية عالية الجودة, تقديم شعور مرضي يعزز تجربة المستخدم الإجمالية. بالإضافة إلى ذلك, يساهم الملمس في جاذبية الحقيبة البصرية, جذب المستهلكين الذين يقدرون الحرف والفن المعنية.
المواد اللازمة لصنع الأكياس الجلدية
تتضمن عملية صنع الأكياس الجلدية مجموعة مختارة بعناية من المواد واللوازم التي تضمن الوظيفة والجاذبية الجمالية. سيستكشف هذا القسم المواد والأدوات الأساسية اللازمة لإنتاج الأكياس الجلدية الفعالة.
مواد صنع الأكياس الجلدية
تلعب المواد المستخدمة في الأكياس الجلدية دورًا حيويًا في تحديد الجودة الشاملة ومتانة المنتج النهائي. وتشمل المكونات الرئيسية:
- بطانات: القطن, البوليستر, صقيل
- الأجهزة المعدنية: أبازيم, الخواتم, المشابك
- السوستة: معدن, البلاستيك
- خيط: البوليستر, نايلون
حقائب جلدية أساسية لصنع المصانع
بالإضافة إلى المواد المذكورة, تتطلب المصانع مجموعة من الإمدادات المتخصصة لضمان إنتاج فعال. وتشمل هذه الأدوات والمعدات الأساسية:
- أدوات القطع: قواطع دوارة, السكاكين, موت
- آلات الختم: الطوابع الزخرفية, أدوات العلامات التجارية
- أدوات الخياطة: آلات الخياطة, أدوات غرز اليدين
- لاصق: المواد اللاصقة القائمة على الماء, الأسمنت الجلدي
عملية صنع الأكياس الجلدية في المصانع
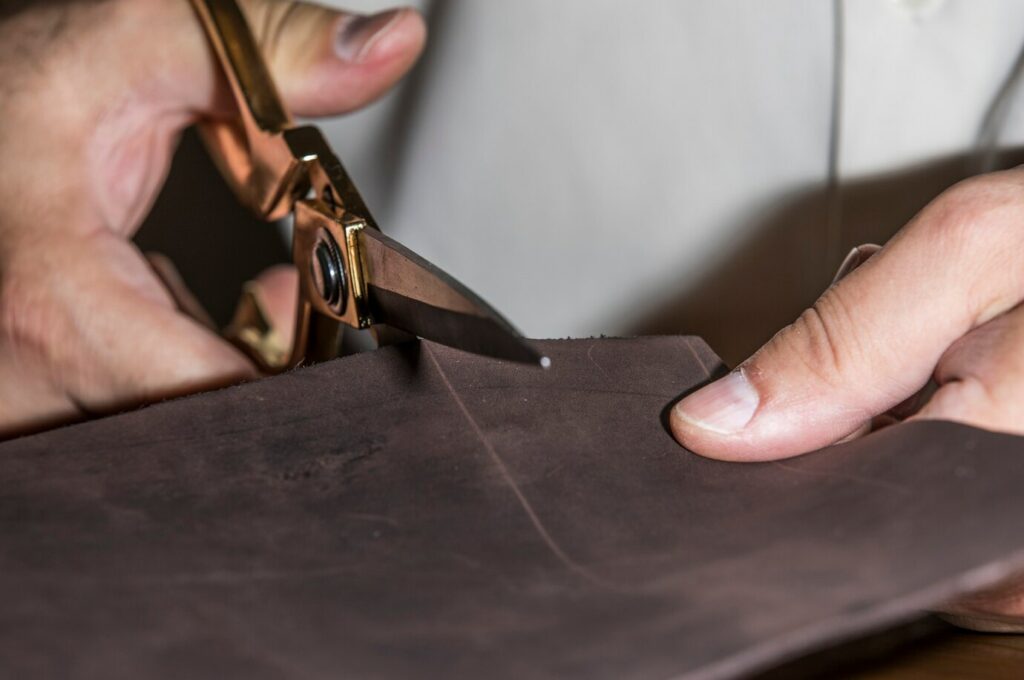
ال عملية صنع الأكياس الجلدية في المصانع ، تتضمن سلسلة من الخطوات الدقيقة التي تحول المواد الخام إلى منتجات تامة. كل مرحلة أمر بالغ الأهمية لضمان الجودة والحرفية, مما أدى إلى أكياس جلدية جميلة وعملية. فيما يلي نظرة عامة على الخطوات الأساسية في هذه العملية.
خطوة 1: تصميم وجعل نمط
تبدأ الرحلة بمرحلة التصميم, حيث يتخيل مفهوم الحقيبة. يقوم المصممون بإنشاء رسومات مفصلة تحدد بنية الحقيبة, أبعاد, والميزات. بمجرد الانتهاء من التصميم, تم تصميم نمط. هذا النمط بمثابة قالب لقطع الجلد وعادة ما يكون مصنوعًا من مواد متينة مثل الورق المقوى أو البلاستيك.
خطوة 2: قطع الجلد الخام
يعد قطع الجلد الخام خطوة حاسمة تتطلب الدقة. عادة ما تستخدم المصانع ثلاث طرق:
- قطع الليزر: تستخدم هذه التقنية شعاع ليزر مركّز لقطع الجلود بدقة رائعة. يتم توجيه الليزر ببرامج الكمبيوتر التي تتبع النمط المصمم في وقت سابق, السماح بتصميمات معقدة وحواف نظيفة. يمكن أن تقطع حرارتها الشديدة الجلد وتغلق الحواف, تقليل التلاشي والحاجة إلى تشطيب إضافي. والنتيجة هي قطع دقيق للغاية يقلل من النفايات ويسمح بأنماط معقدة, مما يجعلها مثالية للتصميمات التفصيلية والدفعات الصغيرة.
- يموت قطع: يتضمن قطع الموت استخدام ممولة متخصصة - بشكل ضروري على شكل قالب مثل النمط المطلوب - لكمة القطع من الجلد. يتم الضغط على الموت على الجلد بقوة كبيرة, خلق أشكال موحدة. إنه فعال بشكل خاص للإنتاج الضخم, لأنه يسمح بتخفيضات ثابتة عبر كميات كبيرة من المواد.
- قطع اليد: غالبًا ما يختار الحرفيون الماهرون قطع اليد, خاصة بالنسبة للتصميمات الفريدة أو المفصلة. تتضمن هذه الطريقة استخدام سكين قطع أو قاطع دوار, السماح للحرفيين بممارسة السيطرة الكاملة على عملية القطع. في حين أن هذا النهج يستغرق وقتًا طويلاً وكثافة العمل, إنه يوفر إمكانية لمستويات عالية من التفاصيل والتخصيص. يمكن أن يكون لدى القطع المقطوعة يدويًا شعورًا أكثر حرفيًا, مع اختلافات طفيفة تعزز تفردها.
خطوة 3: غرز الحقيبة الجلدية
بمجرد قطع الجلد, الخطوة التالية تتضمن خياطة حقيبة جلدية. يمكن تحقيق هذه العملية باستخدام طرق مختلفة:
- غرزة السرج: غرزة السرج هي طريقة تقليدية مفضلة لقوتها ومتانتها. أنه ينطوي على استخدام اثنين من الإبر, كل خيوط من خلال نفس الفتحة من الجانبين المعاكس. هذا يخلق غرزة متشابكة آمنة أقل عرضة للفك, حتى تحت الضغط. غالبًا ما يتم استخدام غرزة السرج في أكياس جلدية عالية الجودة, لأنه لا يوفر المتانة فحسب ، بل يضيف أيضًا لمسة حرفية إلى الحرف اليدوية. التماس الناتج مرئي ويضيف شخصية إلى الحقيبة.
- غرزة قفل: يشيع استخدام غرزة القفل في آلات الخياطة وتتضمن متشابكين خيطين, واحد من الأعلى والآخر من القاع. هذه الطريقة فعالة للإنتاج ذو الحجم العالي, تقديم إنهاء أنيق ومتسق. في حين أنه قد لا يوفر نفس مستوى القوة مثل غرزة السرج, إنه مناسب للعديد من أنواع الأكياس الجلدية ويسمح بتجميع أسرع.
- خياطة اليد: يوفر خياطة اليد درجة عالية من السيطرة والتخصيص. يستخدم الحرفيون الإبر والخيط لخياطة الجلد يدويًا, السماح بتصميمات معقدة ولمسات فريدة. هذه الطريقة تستغرق وقتًا طويلاً ولكنها تؤدي إلى منتج فريد من نوع. غالبًا ما يتم استخدام خياطة اليد في أكياس جلدية مخصصة, حيث تكون الحرفية والاهتمام بالتفاصيل أمرًا بالغ الأهمية.
- خياطة الآلة: تستخدم هذه الطريقة آلات الخياطة لأتمتة عملية الخياطة. خياطة الآلة مثالية للإنتاج الضخم, توفير نتائج وكفاءة متسقة. يمكن استخدام أنواع مختلفة من غرز الماكينة, بما في ذلك مستقيم, متعرج, والغرز الزخرفية. في حين أن خياطة الماكينة يمكن أن توفر مظهرًا موحدًا, قد يفتقر إلى الشعور الحرفي بالطرق المخيمة يدويًا.
خطوة 4: تجميع المواد وربطها
تعد مرحلة التجميع والبطانة خطوة محورية في عملية صنع الأكياس الجلدية, نظرًا لأنه يجمع جميع المكونات التي تم إعدادها مسبقًا لتشكيل منتج متماسك وعملي. تتضمن هذه المرحلة اهتمامًا دقيقًا بالتفاصيل لضمان أن الحقيبة تبدو جذابة وتلبية المتطلبات العملية.
- إعداد المواد: قبل التجميع, جميع القطع الجلدية, بطانات, يجب تنظيم المكونات الأخرى وإعدادها, مع مواد بطانة مشتركة بما في ذلك القطن, البوليستر, وساتين. يتضمن ذلك التحقق من أي عيوب في الجلد والتأكد من أن مادة البطانة تكمل التصميم الخارجي.
- إرفاق البطانة: عادة ما يتم قطع البطانة لتناسب الأبعاد الداخلية للكيس. ثم يتم خياطة أو لصقها إلى السطح الخارجي للجلد. اعتمادا على التصميم, قد يغطي البطانة جميع الأسطح الداخلية أو تقتصر على مناطق محددة.
- تجميع المكونات: مع البطانة في مكانها, تتضمن الخطوة التالية تجميع المكونات المختلفة للكيس, مثل الجيوب, اللوحات, والأشرطة. يتم محاذاة كل قطعة بعناية وتأمينها باستخدام خياطة أو لاصق. إذا كان التصميم يتضمن جيوبًا أو مقصورات, يتم إضافتها خلال هذه المرحلة, توفير الوظائف والتنظيم داخل الحقيبة.
- التحقق من المحاذاة وملاءمة: مع تقدم الجمعية, من الضروري التحقق من المحاذاة باستمرار وتناسب جميع المكونات. يمكن أن يؤثر أي اختلال على المظهر العام للكيس ووظائفه.
- التعديلات النهائية: مرة واحدة تجميع, يمكن إجراء أي تعديلات نهائية لتعزيز هيكل الحقيبة. قد يشمل ذلك مناطق التعزيز التي ستحمل معظم الإجهاد, مثل مرفقات المقبض أو نقاط الإغلاق.
خطوة 5: إنهاء حافة الحقيبة الجلدية
اللمسة النهائية تنطوي على علاج الحافة, وهو أمر حيوي لكل من الجماليات والمتانة. تشمل التقنيات:
- الطلاء الحافة: تتضمن لوحة الحافة تطبيق طلاء متخصص أو إنهاء على الحواف الخام للجلد. توفر هذه التقنية سلسة, نظرة مصقولة أثناء منع الجلود من التلاشي. طلاء الحافة متوفر بألوان مختلفة, السماح للمصنعين بمطابقة أو التباين مع السطح الخارجي للكيس لأغراض جمالية. يتطلب تطبيق الطلاء الحافة الدقة, في كثير من الأحيان استخدام الفرش أو التطبيقات لضمان معطف حتى. بعد التطبيق, قد يُسمح للحواف المطلية بالتجفيف قبل أن يتم تجفيفها من أجل الانتهاء من اللامع, تعزيز المظهر العام للكيس.
- حافة الحافة: الحافة المائلة هي عملية تقليص وتجديد حواف الجلد لإنشاء ليونة, نظرة أكثر دقة. هذه التقنية لا تحسن جماليات الحقيبة فحسب ، بل تقلل أيضًا من احتمالية اصطياد الحواف على الأشياء أو التلاشي مع مرور الوقت. يستخدم الحرفيون الماهرون أدوات مشطولة لتشكيل الحواف بعناية, مما أدى إلى انتقال سلس من سطح الجلد إلى الحافة. يمكن الجمع بين الرسم مع اللوحة الحافة للحصول على لمسة مصقولة ترفع براعة الكيس.
خطوة 6: تلميع سطح الجلود
الخطوة الأخيرة في عملية صنع الحقيبة الجلدية هي تلميع سطح الجلود. هذه الخطوة تعزز مظهر الحقيبة وتحمي المواد. يتم توظيف تقنيات مختلفة, مشتمل:
- تلميع: الشفق هو عملية تجانس حواف الجلد لإنشاء لمسة مصقولة. غالبًا ما تتضمن هذه التقنية استخدام أداة محطمة أو قطعة من القماش لتطبيق الاحتكاك على الحواف, مما أدى إلى مظهر أنيق ولامع.
- التزجيج: يوفر تطبيق التزجيج لمسة نهائية لامعة على سطح الجلد, تعزيز لونه وعمقه. تتضمن هذه التقنية نشر طبقة رقيقة من التزجيج بالتساوي على الجلد, السماح له بالتجفيف والعلاج.
- الشمع: يعمل الشمع على حماية الجلد من الرطوبة والأوساخ أثناء إضافة لمعان خفي. يتم تطبيق الشمع عالي الجودة على السطح, إنشاء حاجز يساعد في الحفاظ على سلامة الجلد مع مرور الوقت. هذا العلاج يغذي الجلد, إبقائه مرنًا ومنع التكسير.
- برتقالي: يستخدم التلقي قطعة قماش ناعمة أو فرشاة لفرك سطح الجلد برفق بعد تطبيق الشمع أو التلميع. هذه الخطوة تعزز تألق وسلاسة الجلد, إعطائها الانتهاء من.
- بولندي: يضيف تلميع الجلد طبقة إضافية من اللمعان والحماية. عادة ما يتم تطبيق البولندية الجلدية باستخدام قطعة قماش ناعمة, عمله في الجلد لتعزيز لونه وملمعه.
- زيت: يساعد تكييف الجلد بالزيت على الحفاظ على ليونة ومنع التجفيف. زيوت جلدية تخترق المادة, توفير الرطوبة والتغذية.
- صبغ: إذا كان الجلد يتطلب تعديلات ألوان أو ترميم, يمكن استخدام الصباغة. تتضمن هذه العملية تطبيق صبغة جلدية لتحقيق اللون المطلوب مع الحفاظ على نسيج الجلد.
مراقبة الجودة في مصانع الأكياس الجلدية
ضبط الجودة أمر ضروري في تصنيع الأكياس الجلدية لضمان تلبية المنتجات معايير عالية. تتضمن هذه العملية عمليات تفتيش شاملة وطرق اختبار محددة.
فحص الجودة واتساق الخياطة
- التفتيش البصري: يفحص المفتشون الجلود للعيوب مثل الخدوش أو الملمس غير المتكافئ. يتم فحص كل حقيبة بصريا لحوالي 3-5 دقائق لالتقاط أي عيوب.
- فحص خياطة: يقوم المفتشون بتقييم الخياطة من أجل الاتساق, فحص حتى التباعد والحلوف الضيقة.
- اختبار اللمس: يتم فحص سطح الجلد للحصول على بقع أو تناقضات خشنة.
اختبار المتانة والوظائف قبل التوزيع
- اختبار الإجهاد: تتعرض المقابض والشرح للوزن. على سبيل المثال, قد يتم تحميل الحقائب مع 10-15 الجنيه ويخضع لاختبارات التوتر ل 5 دقائق لتقييم القوة.
- اختبارات السوستة: المفتشين يفتحون السحابات وإغلاقهم 50 مرات لضمان التشغيل السلس. هذه العملية تأخذ حولها 5 دقائق.
- اختبار تحمل الوزن: يتم تحميل الحقائب بأوزان تساوي استخدامها المقصود, وعقد ل 10 دقائق لتقييم مدى الصيانة تحت الضغط.
- فحص الوظيفة: يتم اختبار المقصورات والإغلاق لسهولة الاستخدام والوصول.
نصائح إضافية: عملية تصنيع الأكياس الجلدية المستدامة
يعد اعتماد ممارسات مستدامة في عملية تصنيع الأكياس الجلدية أمرًا ضروريًا لتقليل التأثير البيئي وتعزيز الإنتاج الأخلاقي. فيما يلي بعض النصائح الرئيسية للمصنعين التي تهدف إلى تعزيز الاستدامة:
- المصدر الجلود الأخلاقية: سيختار بعض الشركات المصنعة مثل Novote الجلود من الدباغة التي تلتزم بالممارسات الصديقة للبيئة, مثل استخدام أساليب جلد الألياف الدبنية والخضروات بدلاً من المواد الكيميائية الضارة. هذا يقلل من التلوث ويقلل من النفايات الكيميائية.
- استخدام المواد المعاد تدويرها: قد يدمج صانعو المواد المعاد تدويرها أو مواد معاد تدويرها في تصميمات الأكياس. يمكن أن يشمل ذلك استخدام بقايا من منتجات جلدية أخرى أو دمج الأقمشة المعاد تدويرها للبطانات والمكونات.
- تنفيذ العمليات الموفرة للطاقة: قد يستخدم صناع الآلات الموفرة للطاقة ومصادر الطاقة المتجددة في مرافق الإنتاج. هذا يساعد على تقليل بصمة الكربون المرتبطة بالتصنيع.
- تقليل استخدام المياه: سيتم اعتماد التقنيات التي تتطلب كميات أقل من المياه أثناء عمليات الدباغة والصباغة. يمكن لتنفيذ أنظمة الحلقة المغلقة إعادة تدوير المياه, مزيد من الحد من الاستهلاك.
- احتضان التصميم المعياري: قد يصنع صناع الحقائب ذات المكونات القابلة للاستبدال, مثل الأشرطة والشرح, السماح للمستهلكين بالإصلاح بدلاً من تجاهلهم. هذا يعزز الاقتصاد الدائري ويمتد عمر المنتج.
كيف يساعد Novote أعمال حقيبتك الجلدية?
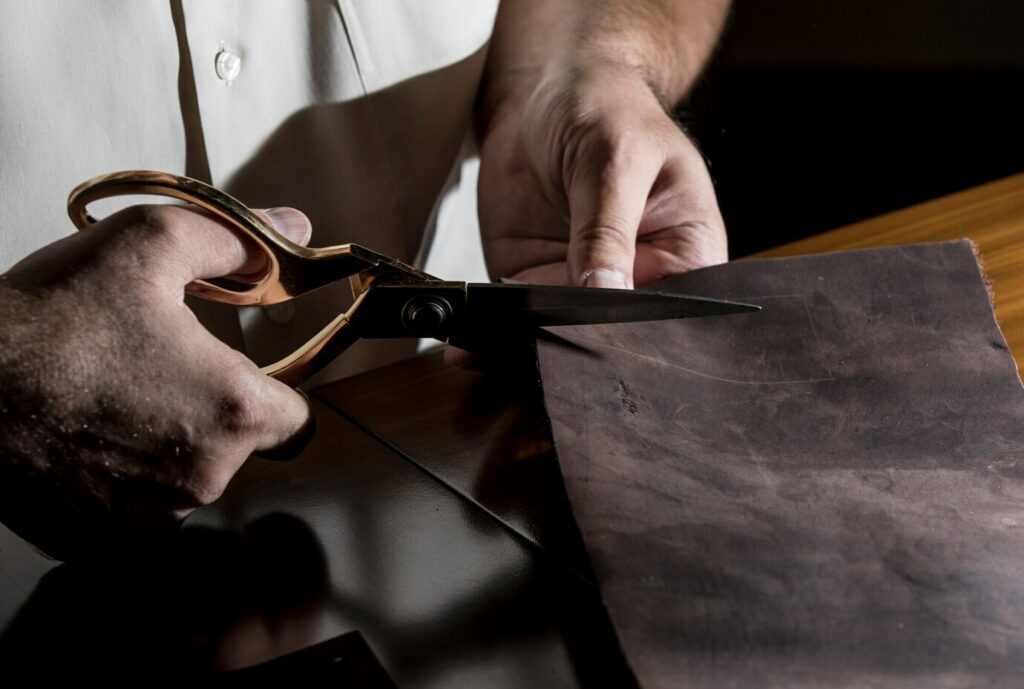
NOVOTE, علامة تجارية لعلامة سفر جلدية مملوكة لشركة Tinlee Group, يقف في طليعة الصناعة, متخصص في حقائب جلدية مخصصة بالجملة. مع الالتزام بالابتكار والجودة, أكياس جلدية سفر محايدة بين الجنسين الحرف اليدوية باستخدام جلد البقر الممتاز والجلد الدقيق. هذا المزيج الفريد لا يعزز المتانة فحسب ، بل يفي أيضًا بالتفضيلات المتنوعة للمستهلكين المعاصرين.
في قلب نجاح نوفوت هو مخصص ص&فريق D., تضم 30 ركز المتخصصون على تصاميم الاتجاه. من خلال دمج جلد الألياف الدقيقة مع نسيج نايلون مقاوم للماء, يقوم Novote بإنشاء أكياس ليست أنيقة فحسب ، بل تعمل أيضًا في سيناريوهات السفر المختلفة.
لزيادة تعزيز رضا العميل, يقدم Novote ضمان ضمان الجودة لمدة عام واحد. تؤكد الشركة أيضًا على أهمية أخذ عينات ما قبل الإنتاج, ضمان أن كل ترتيب كبير يكرر التصميم المقصود 1:1. يمكن للعملاء توقع تسليم عينة سريعة داخل 7-10 أيام العمل, مع أوامر بالجملة جاهزة داخل 25-35 أيام العمل. لأولئك الذين يحتاجون إلى خدمات عاجلة, أوامر الاندفاع متاحة أيضا.
خاتمة
تشمل عملية صنع الأكياس الجلدية مزيجًا غنيًا من المواد, التقنيات, والفن الذي يتوج بمنتجات وظيفية وأنيقة. عن طريق الخوض في مراحل الإنتاج المختلفة, من التصميم إلى مراقبة الجودة, نكتسب تقديرًا أكبر للحرفية المعنية. لأي شخص مهتم بالحقائب الجلدية, يمكن أن يؤدي استكشاف الممارسات المستدامة إلى زيادة تعزيز مجموعتك مع دعم المبادرات الصديقة للبيئة.
التعليمات
س 1: ما هي المواد الخام للأكياس الجلدية?
تشمل المواد الخام الأولية للأكياس الجلدية أنواعًا مختلفة من الجلد, بطانات, الأجهزة المعدنية, وخيط قوي. كل مكون ضروري لضمان المتانة, الوظيفة, والجاذبية الجمالية.
Q2: ما الذي يجعل حقيبة جلدية عالية الجودة?
تتميز حقيبة جلدية عالية الجودة بمتانتها, المرونة, والملمس. جلد عالي الجودة, الحرف الدقيقة, والاهتمام بالتفاصيل في خياطة وإنهاء كل شيء يساهم في الجودة الشاملة للكيس.